Chemical nickel plating
is a method of metal surface treatment that is widely used in industry. Also known as electroless nickel plating, this technology offers unique features that distinguish it from the traditional electroplating method.
Principle
This is a process in which a layer of nickel and phosphorus is deposited on the surface of a metal object without the use of an electric current. It uses an autocatalytic reaction in which nickel is reduced from a solution containing nickel salts with the aid of a reducing agent. This reaction takes place uniformly over all surfaces of the components immersed in the bath. Unlike electroplating, chemical nickel plating ensures a uniform thickness of the metal coating on the surface of the plated parts, even in internal cavities and on parts with complex geometries.
Chemical nickel plating is used in a wide range of industries:
- Automotive industry
- Aerospace industry
- Engineering
- Electronics
- Food and pharmaceutical industry
We offer laboratory chemical nickel plating of copper, steel and aluminium alloys, with the following properties of the excluded coatings:
- The thickness of the nickel coating usually ranges from 1-100 µm
- Phosphorus content: 4-8 %
- Basic hardness: approx. 400 HV
- Hardness after heat treatment by us: up to 1000 HV
- Slightly magnetic to non-magnetic surface finish
- Low coefficient of friction, excellent corrosion protection and high abrasion resistance
- The plated surface has an attractive semi-gloss to glossy appearance
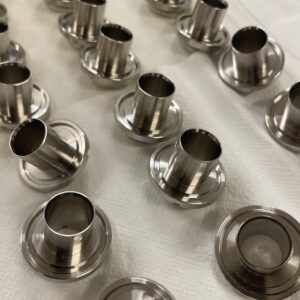
Need something to pony up? Do not hesitate to contact us.
Follow us on our social networks. Find us on Facebook and Instagram.
Electroforming s.r.o. – We meet individual requirements from development to production.