History and origin of electroforming
The Czech name “galvanoplastiky” comes from the Russian term for this technology and refers to its original application in the fine arts. This name can be misleading as it has nothing to do with plastics. Electroforming was discovered in 1836 by the German-Russian scientist Moritz Hermann Jacobi. Since then, it has been used not only to produce works of art (metal sculptures), but also in many industries.
Principle
Electroforming, or galvanoplasty, is a technology that has been known and used for many decades. Its principle is the electrodeposition of metal layers on the surface of the primary model. With the help of electrolysis, this process allows metal layers ranging from tens of micrometres to units of millimetres to be removed.
The primary model is usually made of a material such as metal, plastic, modeling compound, or other suitable material. The model is most often removable, which creates a precise metal imprint of the original model (galvano) or hollow part (shell). Components or products produced in this way are often difficult or even impossible to realize using classical engineering methods.
The most used metals in electroplating are copper and nickel. Depending on the desired properties of the final product, other metals such as silver or gold can also be used. The resulting products can also be created by combining different metals or a single metal with different physical properties.
Electroforming step by step
- Preparation of the primary model: In order to allow electrochemical processes to take place, the surface of the model is is modified to be electroconductive,
- Metal layer deposition: the electrically conductive model is immersed in an electrolyte, where it acts as a negative electrode (cathode) and a metal layer is deposited on its surface by passing a DC electric current. This process can take several hours or even days, depending on the desired thickness of the metal.
- Removing the model: After the required thickness of the metal layer is reached, the plated model is removed from the bath. The next step is to separate the galvano from the model to create a self-supporting metal product.
- Finishing operations: Finally, the galvano is cleaned and further machined as required, which may include grinding, polishing or other surface or shape modification operations.
Applications of electroforming
Electroforming finds a wide range of applications in various fields today:
- Engineering: tools and moulds, gauges, electrodes, heat exchangers,
- Aerospace: manufactures combustion chambers, composite materials and strength elements,
- Automotive: masking stencils, moulds for moulding dashboards, lights and other parts,
- Electrical engineering: manufacture of microwave components, heat sinks, and other special conductive structures,
- Fhysics: allows the manufacture of mirrors, optical components, parabolas and other precision elements,
- Music industry: tools for pressing CDs and vinyl records,
- Glass industry: used for the production of moulds and grinding tools.
- Conservation and art: replicas of badges, seals, medals, GalvanoPhoto
Examples of electroforming applications:
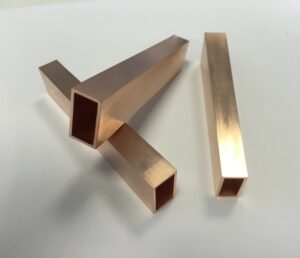

Electroforming can also be used for “cold welds”, which are used for joining metal parts without thermal diffusion of particles between the parts. Examples include the joining of microwave waveguide tubes with flanges (without the need for gluing or soldering), the production of special metal-in-metal electrodes for welding machines, the production of targets for vacuum technology, etc.
With a suitable model design, it is also possible to forge pre-prepared beams, cooling and heating structures, or even ejectors or casting channels into the newly created galvanoplastic formations.
Refurbishment and repair of manufacturing errors
An interesting area is the refurbishment or repair of defects in metal parts, where the missing metal is added cold and the part is not subjected to thermal stress in volume (as in conventional welding) or surface (as in laser welding or metal spraying).
Combining tradition with innovation
Modern electroforming (galvanoplasty) is a combination of traditional processes together with modern technologies. Electroforming not only expands the possibilities of production, but also brings new perspectives to the world of industry and art. If you are interested in learning more about this technology and its applications, stay tuned for more news and stories from our work.
Electroforming s.r.o.
– We meet individual requirements from development to production.